Outdoor Buildings: Do It Yourself
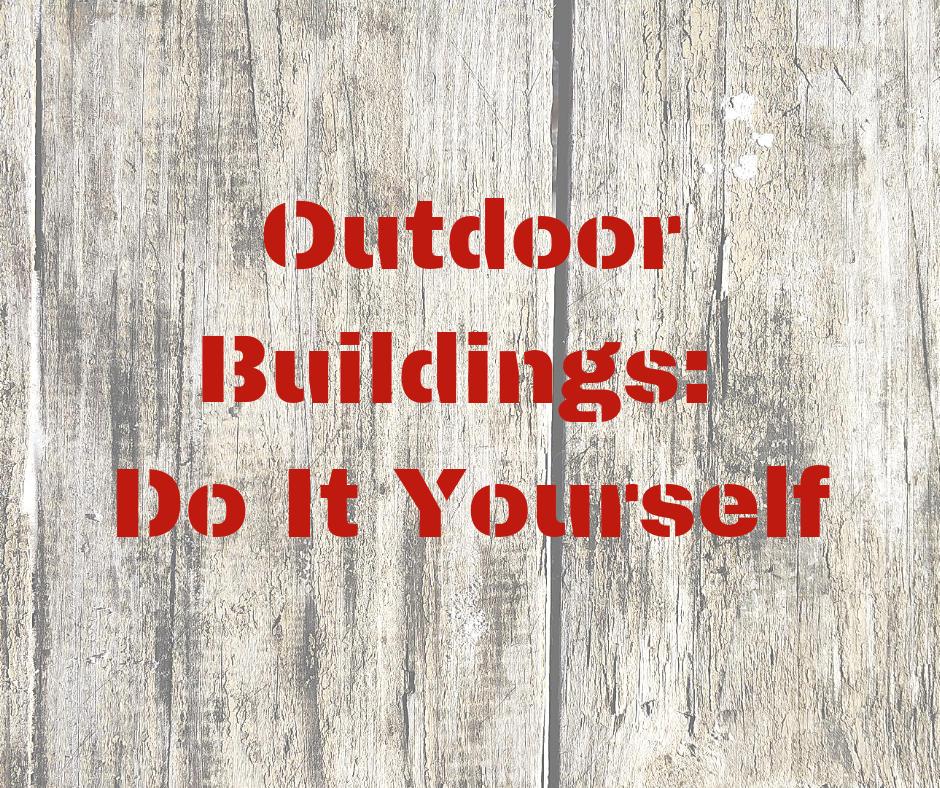
Outdoor Buildings: Do It Yourself
Published at June 26 2025 by JFord
It’s summertime and that means time to find the pool floaties, noodles, life vests and swim shoes. So, you go through your house hunting these like Elmer Fudd. After hours of searching and the kids asking every five minutes, “Can we go swimming, yet?", you finally uncover them. They were under the Easter decorations and on top of the Halloween decorations. And you realize something. You just don’t have enough space. So, what do you do?
If you are like me and my husband, then you decide to build you an outdoor building. Luckily, we just did this type of project a couple of years ago. I can tell you some tips and tricks to help make your building project run a little more smoothly than ours did.
Stage One: Planning
The first thing you want to do is decide how large you want the building to be, what type of building it is going to be and where you are going to build it. At first, we thought about building just a pole barn. These are usually open on 2 to 3 sides and have a dirt floor. We decided against that. I don’t like dirt floors and we wouldn’t have any way to secure our tools
So, we decided to go with what we now call a mini barn. It’s 1.5 stories and has a barn style roof that allows you to stand almost for the entirety of the loft. We planned the size so that we wouldn’t have to make many cuts in our materials. I don’t remember the exact measurements, but I believe each side is 12 foot long.
Once you have the idea of what you want to build and how large it’s going to be, you’re going to have to pick a location. We decided to build ours on the sunny side of our lot. We don’t have many trees on the lot, so we wanted to take up some of the open sunny area with the building. It’s also a location that has good drainage.
Once you have all of that mapped out, you need to visit with your local planning commission. If you need a permit, now is the time to buy it. There also may be restrictions on how large of a building you can have and where in your lot it will be placed.
Stage Two: Buying Materials
The biggest thing that I can tell you in this stage is to buy materials for each stage as you build it. Unless you have somewhere to store the materials while you are working on the building, the materials are going to be sitting out in the weather and that’s not good.
Also, buy good materials. For anything that is going to be on the ground floor or near the ground, make sure you have ground contact lumber. This means that it is resistant to mold and insects and that it will last longer in these conditions.
Two things you want to make sure to buy a lot of in the beginning are nails and brackets. You have no idea how many nails it takes to build a building. It takes a lot! So, make sure to just buy the big bucket of them. Brackets are the same way. These are an easy way to make sure that your structure is strong. So, make sure you have plenty of them.
You’re also going to need assorted hand tools like hammers, tape measures, circular saw and pencils to mark with. We went ahead and got a small power hammer. It made doing the walls so much easier.
Stage Three: Foundation and Floor
Now if you just want to have a dirt floor, you can skip this part. I personally think that dirt floors are useful in places where you don’t get much precipitation or if the location is one where the drainage is really good. But they do attract insects and you can have more problems with your building settling later.
If you don’t want to have just a dirt floor, there are two ways to build an outdoor building’s foundation and floor. The first is to put in a concrete pad and the second is the use a pier system and build a subfloor.
Concrete PadIf you want to have a concrete pad, you are more than likely going to have to have a professional put it in for you. Concrete is one of those things that you have to future proof and plan meticulously or it doesn’t work for the long term.
If you want to have plumbing or electricity run through the floor you are going to need to put in all of the wiring and piping prior to having the concrete poured. You’ll also want to make sure that the ground where you are pouring the concrete is completely bare and as evenly filled as possible. Once the professionals come to pour the concrete, they will build a wooden frame to hold the concrete in place, pour the concrete, smooth it out and make sure its even.
Then you have to let the concrete set and cure. It’s not an overnight process. Sometimes, depending on the humidity in the area that you are building, it can take weeks or even months for concrete to cure properly. But this isn’t something that you want to rush. Concrete that hasn’t been cured properly will settle unevenly and sometimes crack.
Wood FloorIf you are building a wood subfloor, then you are going to have to do something a bit different. You are basically going to create a mini pier foundations system for your building. You’ll want to have a block on each corner and spaced evenly throughout the foundation of the building.
To put each block down, you need to make sure that the area is clear and as level as possible and that you have gravel put down under each block. The gravel helps to keep the ground in place and keeps water from pooling up under your building.
Then you’ll want to take a level and make sure that not only each block is level but that the structure will be level as a whole. We have a slight grade on our property so one side of the building has a higher stack of blocks than the other to make it sit level.
To build the subfloor, we built a frame and made sure it was square. Then we put in cross braces every 16 inches. This will vary depending on the building codes in your area, but our research told us that this was a standard width for cross braces. Not on did we nail them in, but we used brackets to help hold them together more securely.
Once we had the frame and cross braces completed, we put down two alternating layers of heavy-duty plywood. This is the basis of our floor. We wanted to make sure that we put down two layers, because we were going to be parking the lawn mower and trimmer in the building and wanted to make sure it could sustain the weight.
Stage Four: Building the Walls
Building the walls was one of my favorite things about this project. Once you got into the rhythm of doing it, it became very easy and they went together very quickly. To build a wall, you take two long boards and lay them parallel to one another. Then you make a big box. Square up the box and start in the middle and nail in more boards vertically 16 inches apart. Or whatever the building code states in your area.
This is when you are going to frame in windows and doors. We don’t have any windows in our shed. This was our first major building project and we just didn’t think about trying it until we were done with it. We also only have one door.
Once you have at least two of the walls build you can actually start raising them and attach them to the foundation. While you are still raising the walls and attaching them, you’ll want to brace them to keep them from falling. They are only completely secure when all four of them are up.
To attach the walls to the floor you are going to use large bolts that will go through the bottom board (bottom plate) and into the floor itself. If you have a concrete pad, it may be better to go ahead and drill the hole out before you raise the walls. Concrete can be a bit tough to get through.
Once you have the walls raised and attached to the floor and to each other, you can put plywood boards up on the outside of the building. If you really want to get fancy, like we did, you can then put a siding of some sort on the outside of that. We wanted to make sure that the typical Arkansas humidity wouldn’t take our building out of commission too early.
Stage Five: The Roof
Now we actually put in a loft on our building. That would ordinarily come next. The process was essentially the same as it was to build the floor, but we just attached it to the walls instead of to the foundation. We’re going to assume that you are not building a second floor.
So now its time to think of rafters and the roof. Honestly, if we had to do it over again, we would have gotten the rafters professionally done or bought them prefabricated. They were the absolute worst part of the whole process. I don’t think any of our rafters came out completely right. So, take my advice and have someone do them for you or get them premade.
After you get the rafters in place, you will want to put in the cross bracing. The cross bracing helps the roof remain stable and it will run the length of the building under the rafters. Then you can put in the end pieces. These also brace up the rafters and give your building a nice closed off feeling. (I don’t like heights.)
Once you have all of that done, you can put in some boards to be the basis of the roof. Once again, we used plywood sheets that we cut to size. They weren’t terribly heavy, and we were able to secure them quite easily.
Over the plywood you’ll want to run tar paper or some sort of moisture barrier. This will help keep water from accumulating under the shingles and help your building last longer.
The last step in the roof is to, well, put a roof on. We used shingles because they were less expensive and easier for us to deal with. You can use shingles or any type of roofing material you like. My husband almost had ours done by the pros. It was quite scary up there.
Stage Six: Doors and Windows
We made a mistake here. We built our door because we wanted something to fit the custom opening that we had made. Unless you have a lot of experience building things, I wouldn’t recommend doing that. I would instead recommend you buy a premade door. That goes for windows as well.
A premade door is going hang better and last longer. That just means that you will have to make the opening to fit it. I still think that is easier than trying to build a door.
Installing a door or window is easy. They basically slide in and get screwed down and you’re done. After this step is just the pretty stuff. We painted ours red with black trim and the door is white with black trim. It’s very striking as you drive up our street and gives our property a Farmville vibe.
If you are looking at building an outside building, just keep in mind that this is not a die-hard step by step tutorial. We used many different resources planning our building and I would hope that you would do the same. This blog does include the basic steps to get you started. Once you have built a building like this, you feel like you can accomplish anything.
Maybe you're looking for a house plan instead? Don’t worry, we have you covered. Come check out Nelson Design Group’s collection of over 1,800 house plans. And come check out the past blog posts in our house plan series:
- Farmhouse style
- Farmhouse House Plans
- Contemporary Modern style
- Contemporary Modern House Plans
- Rustic Style
- Rustic House plans
- Mountain and Cabins House Style
- Mountain and Cabin House Plans
- Examining House Styles: Pool Houses
- House Plan Spotlight: Pool Houses
- Examining House Styles: The Florida Collection
- House Plan Spotlight: The Florida Collection
- Outdoor Buildings: Garages and Pool Houses
Here at Nelson Design Group, we are always ready to make your dream home a reality. If we don’t have the plan that is right for you, we’ll make one. We are experts in our field and have been doing this for over 30 years. Give us a call today and we will be glad to help.

Benefits of Nelson Design Group
If you are looking at building a house, check out our Building Your Dream Home blog series. This series walks you through step by step on how to build a house and is updated regularly.
- Building Your Dream Home: Concept and Design
- Building Your Dream Home: Loans and Permits
- Building Your Dream Home: Site Prep and Grading
- Building Your Dream Home: Foundations and Underground Utilities
- Building Your Dream Home: Framing
- Building Your Dream Home: Roofing
- Building Your Dream Home: Rough-In
- Building Your Dream Home: Exterior Doors
- Building Your Dream Home: Choosing Windows
If you haven’t found a builder yet, we have a Find-a-Builder tool right here on our website. These are builders from around the country that we have vetted just for you! They are skilled in their professions and do a great job.
Nelson Design Group has over 1,800 house plans for you to choose from. If you’re unsure about finding what you need, give us a call at (870) 931-5777. Our representatives are always happy to help.
If you are a builder looking to buy plans, sign up for our Builder’s Program. We offer discounts you won’t be able to find anywhere else.
We also have resources that are just for you like access to our Master Planned Communities and Marketing Services.